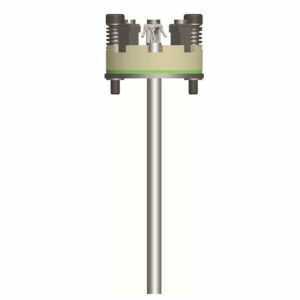
Key Features
Manufactured to IEC 60751
Available with and without transmitters
Mineral Insulated Inset
Designed for ISA-ds 49 style thermowells
Intrinsically Safe designs available
Designed for DIN 43772 thermowells
Markets & Applications
HVAC-R
Chemical and Petrochemical
Energy
Food and Beverage
Oil and Gas
Pharmaceuticals
Ranges
Pt100: -200 ... 600°C
Pt1000: -40 ... 600°C
Accuracy
Class A
Class B
Class AA
Stem length
50 ... 3000 mm
Probe Sheath
Stainless steel 316L (1.4404)
Stem Diameter
1/8", 3/16", 1/4"
3 mm, 4.5 mm, 6 mm, 8 mm
Wiring Configuration
3 wire single or dual
4 wire single or dual
2 wire single or dual
Equipped with a highly reliable and accurate sensing element, featuring the patented Ashcroft® Si-Glass™ sensor, Ashcroft offers a range of differential pressure transmitters specifically designed and developed for use in the cleanroom industry. Using an ultra-thin single crystal diaphragm, Ashcroft differential pressure transmitters offer inherent sensor repeatability and stability, making them stand out as highly accurate, long-term stable and reliable measurement instruments for cleanroom pressure monitoring.
The silicon diaphragm sensor is free of adhesives or other organic materials that are commonly used in differential pressure measurement technology and contribute to a drift in the measured value acquisition or a mechanical reduction in the measurement accuracy.
Ashcroft differential pressure transmitters incorporate the TruAccuracy™ specification. Ashcroft’s accuracy claim is based solely on terminal endpoint methodology and not on statistically derived accuracy claims’.
TruAccuracy™ means that Ashcroft differential pressure transmitters include zero offset, non-linearity, hysteresis, non-repeatability, zero offset and span adjustment error in their accuracy statement.
The user thus has a ready-to-install device at his disposal that does not require any initial calibration after installation. This considerably reduces the time and costs involved.
Other commercially available measuring devices usually do not include information on zero point deviation and span error in their accuracy specifications, so that these measurement errors (up to ±1.00%) must be added to the accuracy in order to achieve reliable performance characteristics.